Webinar
How to Detect Compromised Electrical Connections Under Low Load Conditions
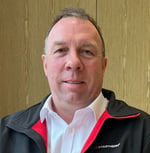
John Hope
Chief Technology Officer
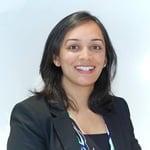
Tulsi Patel
Technical Operations and Support Manager
Americas Timing
12pm Central Daylight Time
Americas Timing
12pm Central Daylight Time
Introduction to Condition Monitoring
The tangible benefits delivered through condition monitoring (CM) of mechanical equipment such as gearboxes, motors, pumps, compressors, rotating machinery, and other similar devices have been globally recognized and adopted for many years.
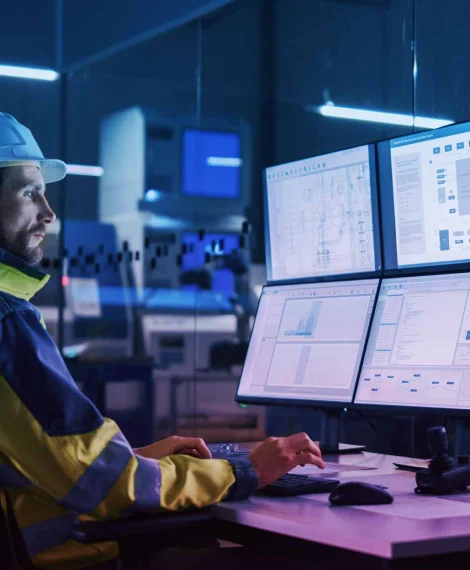
-
Higher productivity
-
Increase asset life expectancy
-
Greater cost efficiencies
-
Optimize maintenance schedules
-
Asset digitization and analysis
-
Improve facility and operator safety
There is growing acceptance that condition monitoring is the most cost-effective maintenance regime – eliminating unnecessary inspection and maintenance costs, as well as detecting up to 70% more failures in advance compared to periodic inspection.
The Risk of Electrical Failure Resulting in Power Outages
Electrical infrastructure is the most critical utility for organizations, irrespective of the industry in question – without power, an organization's activity will be crippled. Regardless of geographic location, an electric power system is vital to energy security, supporting national defense, providing emergency services, critical infrastructure, and the stability of the economy.
The downtime or interruption incurred through an electrical failure can prove costly in the best-case scenarios and disastrous in the worst. For instance, a power failure to a system reliant on strictly controlled temperatures, a relevant example being cryogenic storage for vaccines, could result in the loss of essential inventory and potentially set work back by months or years. In a wastewater facility, it could result in the discharge of raw effluent into a river.
Moving to the world of servers and digitization, the Uptime Institute reports an increasing frequency of downtime costing data centers upwards of $100,000. Outages resulting in more than $1 million have risen from 11% in 2019 to 15% in 2022.
Based on industry surveys carried out by Gartner, the cost of an outage to business averages at more than USD $5k per minute, which equates to over $300k per hour. In the event of an entire day's power outage, organizations would face a colossal cost of more than $8m. It is worth noting that these figures are based on averages, and are ultimately determined by the business environment, risk tolerance, and the vertical market.
Across most industries there has been slow adoption of condition monitoring in electrical infrastructure as a means of identifying potential faults in advance of costly power outages, usually relying on periodic inspections or maintenance to detect such problems.
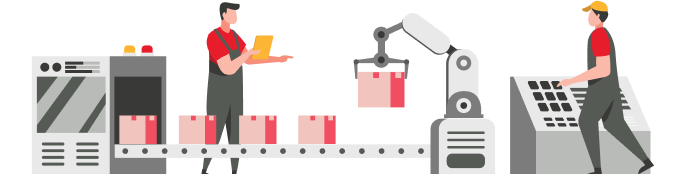
Condition monitoring minimizes the high cost of unnecessary periodic electrical inspections and effectively reduces the typical schedule of maintenance.
Periodic Electrical Inspection
The inspection of electrical equipment is typically carried out at time-based intervals, e.g., quarterly or annually, using thermal imaging cameras. The objective of this type of asset check-up is to reduce the likelihood of an unplanned power outage.
Electrical assessments such as this are carried out by electrical technicians, engineers, and maintenance teams who must wear personal protection equipment (PPE) to inspect assets. This is due to the risks associated with working with electrical equipment where arc faults can be fatal. In many cases, this type of thermal inspection is mandated as a condition of insurance.
The problem with periodic inspection is that checking an electrical asset for functionality and compliance will only validate it for that specific moment in time, as demonstrated by the illustration below It doesn't guarantee the performance of the asset beyond the period in which it is being inspected.
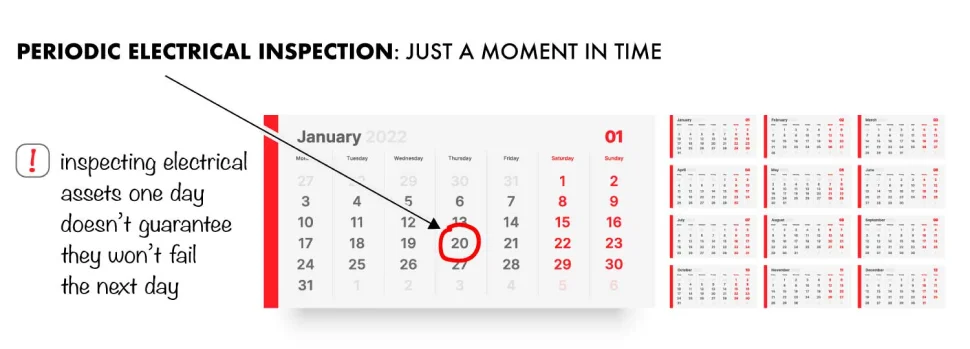
Whilst condition monitoring doesn’t eradicate the need for electrical inspection entirely, it enables the scheduled maintenance of electrical infrastructure to become less frequent. This is a direct result of the availability of condition data to indicate that attention is necessary and that some form of remedial action is required on the equipment.
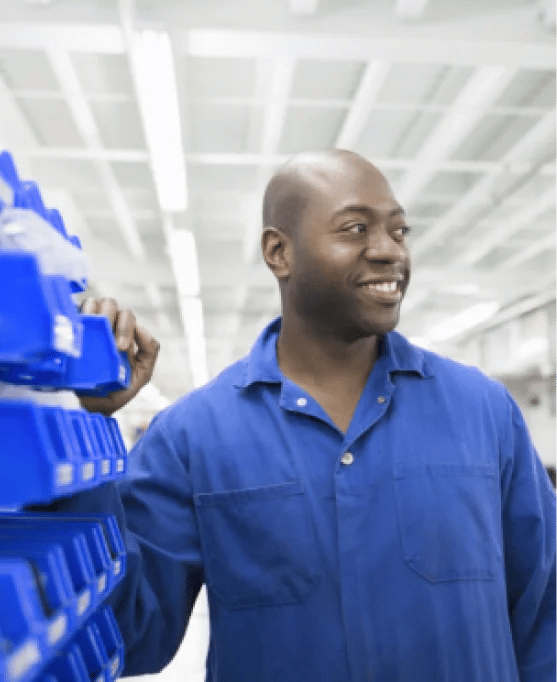
Want to get condition monitoring tips, news and information straight to your inbox? Sign up here.
Digitizing Electrical Infrastructure
Digitization is accelerating the requirement to connect critical equipment and machinery to the internet in order to remotely acquire condition data for subsequent analysis. This is a vital component of the concept referred to as the Industrial Internet of Things (IIOT).
IIOT is not to be confused with the Internet of Things, or IOT, which refers to the billions of devices that are connected to the internet, each performing the task of gathering and sharing data. Whilst similar principles are applicable to both IOT and IIOT as each utilizes the function of digital connectivity and the cloud to share data, the IOT is largely focused on general, or even home use. The IIOT is more focused on connecting and digitizing industrial infrastructure and systems to create the data to boost productivity and deliver more efficient practices.
Connection to the IIOT provides significant commercial benefits. It can grant users a competitive edge in areas such as cost reduction, increased productivity and standardization of best-performing equipment, as well as a host of other advantages.
The commercial benefits of digitization and IIOT are well documented:
Enable uniformity of data across multiple sites
Standardize best-performing equipment
Increase efficiency of procurement process
Reduce critical asset downtime
Eliminate unnecessary inspections or maintenance
Increase safety - remove people from places risk
Improve overall equipment effectiveness (OEE)
Reduce equipment repair / replacement costs
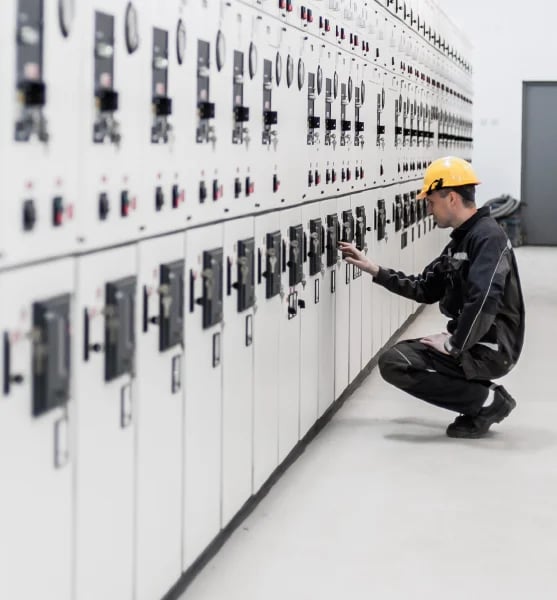
The Purpose of Condition Monitoring
The key objective of condition monitoring can be summarized as the elimination of unnecessary inspections and maintenance by basing intervention on the condition of the equipment. Implementing condition monitoring increases the likelihood of detecting fault symptoms at an early stage, before an issue develops further. Condition monitoring allows for the constant and consistent monitoring of critical assets over time, rather than at a specific point in time.
In summary, the purpose of condition monitoring is to reduce the potential for downtime resulting from failures and the associated repair or replacement of damaged equipment. Obtaining asset data can be carried out remotely, which in turn increases safety by minimizing the need for personnel to interact with electrical infrastructure unnecessarily, reducing the risk in the process.
Online and Offline Condition Monitoring
As businesses strive to improve profitability and deliver higher quality services to their clients, the need to increase productivity has never been greater. In order to maximize production levels, organizations are seeking ways to build in resilience by implementing future-ready assets across critical electrical infrastructure.
The ability to gain insights into the status of critical electrical assets is essential for those responsible for maintaining service uptime. Regardless of industry, ensuring reliable power uptime is key, and changes in asset conditions such as vibration or temperature can indicate potential issues that require attention.
Organizations must ensure assets are equipped to not only to cope with the rigors of today’s production schedules, but tomorrows' and beyond.
The methods used to gain such insights can vary, some opting for occasional or periodic condition inspection, whilst others warrant continuous, permanently installed condition monitoring systems.
Here we outline the fundamental differences between the two primary types of condition monitoring:
- Online condition monitoring can be defined as a continuous or predictive type of process. This type of monitoring is best suited to electrical assets or infrastructure that is critical to business productivity. The constant, uninterrupted nature of this approach to asset management enables the detection of potential issues much earlier. As a result, electrical engineers are able to identify minor problems before they evolve into more substantial faults that compromise services and productivity.
- Offline condition monitoring refers to the process which is occasional, or periodic. This approach is likely to form part of a planned maintenance schedule when concessions can be made to power-down or allow mechanical access to infrastructure. Due to the less frequent nature of inspection, this practice is typically used on electrical components which are less important to productivity or not considered critical to business continuity.
Why is Condition Monitoring Necessary for Electrical Equipment?
Power is central to almost every business across the world today. The World Bank suggests that better long-term investment in power systems is the route to more reliable electrical infrastructure, specifically citing that investing in automated systems to identify network faults and restore service more efficiently is necessary.
As the most critical utility for any organization regardless of the industry, if the power stops, operations stop. Monitoring essential electrical components to ensure the condition is sound will help to avoid unplanned downtime.
The Importance of a Reliable Power Supply
With increasing volumes of data being fed into cloud technologies, the rise of software-as-a-service (SaaS) and the numerous financial systems dependent on resilient service uptime coupled with the unstoppable march of digitization, comes the need for even more reliable system uptime.
Most of the critical functions of businesses today are reliant on a robust power supply, and an electrical outage inevitably results in power loss. From the world’s leading organizations down to the smallest and simplest of operations, power is typically the staple of modern industry and forms the core of manufacturing and production lines.
With condition monitoring technology enabling the advance warning of problems, organizations can reduce instances of downtime, and maximize operational uptime. This is because condition monitoring simplifies the detection of fault symptoms such as electrical hotspots at an early stage of development. For example, the installation of condition monitoring sensors reduces the need for personnel to enter high-risk areas and perform physical maintenance on potentially dangerous equipment.
Condition monitoring will benefit organizations that rely on electrical equipment including:
- Medium and Low Voltage Switchgear
- Motor Control Centers (MCC)
- Dry Resin Core Transformers
- Power distribution units (PDU)
- Uninterruptible Power Supplies (UPS)
- Overhead busbar trunking
- Variable Frequency Drives (VFDs)
- Low Voltage (LV) Transformers
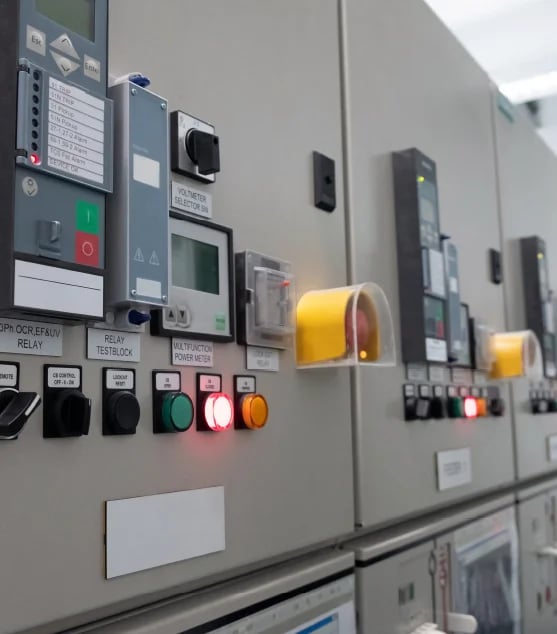
Condition Monitoring and Condition Testing Techniques
There are various forms of condition monitoring, each intended to provide the information required to enable corrective activities on the equipment being observed. Here we outline a selection of commonly used techniques.
Some of the techniques described below constitute continuous monitoring. Others are testing techniques, performed periodically. Sometimes periodic testing and condition monitoring can be carried out at the same time.
There are some jurisdictions that require certain periodic inspections by law, however, these can vary depending on the industry, type of machinery being operated, and the organization’s location. Such statutory inspections are not to be considered maintenance.
Thermal Monitoring
Every moving part in a piece of machinery generates thermal energy or heat. Any component of electrical infrastructure with power flowing through it will also generate heat. Operating machinery will have an acceptable temperature range in which it is supposed to work.
North Electrical Manufacturers Association (NEMA), states that a temperature rise above ambient (Delta T) of 21°C indicates a probable fault. When that value increases to 40°C above ambient it should be regarded as critical and remedial action initiated as soon as possible.
Thermal monitoring utilizes temperature sensors that are permanently installed inside electrical equipment and may include non-contact infrared sensors as shown in the adjacent image, or contact sensors such as thermocouples, thermistors, or resistance temperature detectors (sometimes called a PT100).
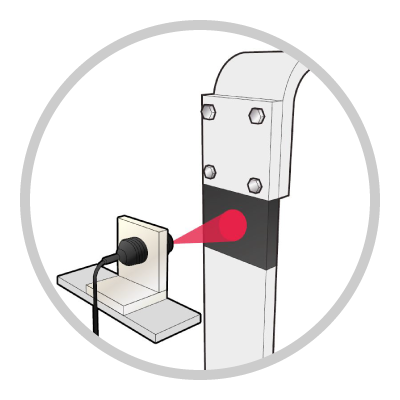
Periodic inspections are considered preventative maintenance and are carried out manually by electrical personnel using infra-red cameras and IR inspection windows. This is an offline technique which provides an inspector with a snapshot in time of asset condition, and should not be confused with online monitoring which provides continuous condition assessment.
Permanently installed sensors monitor temperature conditions at critical points within or around machinery and associated infrastructure. Sensors are capable of collating data from other equipment and compare conditions such as the ambient temperature. The results can be used to generate reports that enable the prediction of equipment most at risk of malfunction or breakdown.
24/7 monitoring of critical electrical assets
Real-time integrated data IIOT future proofing
Increased operator and facility safety
Optimized maintenance = cost savings
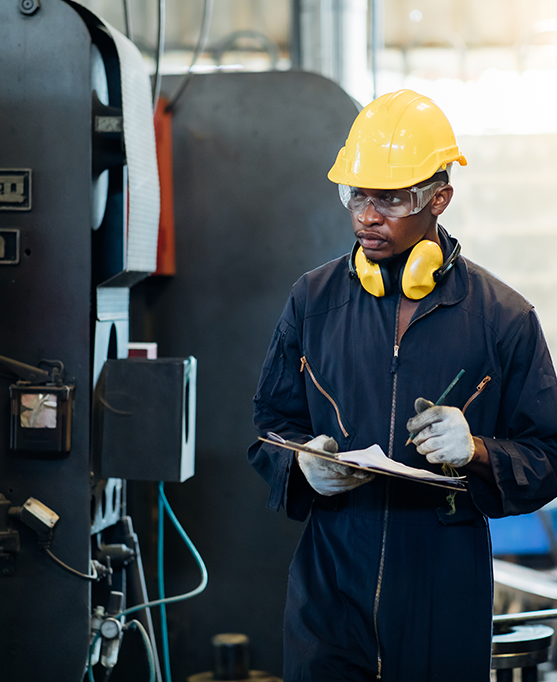
Discover how condition monitoring improves asset reliability across different industries...
Metering
There are thousands of types of meters available globally, and their functionality can range from the basic measuring of a current on a circuit, to more complex examples that include power quality, voltage, harmonics and more.
The main metrics derived from metering can be summarized as:
- Current / amps
- Voltage
- Power factor
- Power quality
- Harmonics
Metering systems measure and record electricity conveyed through a point of connection. Advanced metering systems also have the ability for two-way communication between a meter and a remote system. This can be via a dedicated metering device, or more recently, can be incorporated into circuit breakers.
Electrical Signature Analysis
Electrical signature analysis (ESA) is a non-destructive, non-intrusive method of continuous condition monitoring developed from work done by Oak Ridge National Laboratories primarily to monitor the condition of motor-operated valves in nuclear power plants in the 1980s.
ESA offers the ground-breaking capability to detect and quantify mechanical defects as well as the deterioration of electromechanical equipment and unwanted changes in process conditions. ESA is non-intrusive and doesn't interfere with the operation of equipment whilst being monitored.
Today ESA finds use across a variety of military, commercial and industrial equipment. By linking sensors to the power systems of electro-mechanical equipment ESA systems can detect the variations in current and voltage caused by load and speed variations in the equipment being monitored. Through the data provided by the sensor system, potential faults in the equipment can be diagnosed or even predicted.
Motor Circuit Analysis
A motor power circuit is the section of an electrical motor circuit that delivers high voltage or current to an electric motor. A motor power circuit consists of 4 component parts: a disconnect switch, protective devices (fuses or circuit breakers), a motor starter, and a motor.
Initial checks should be performed on all the essential measures of motor performance: usually, this means testing the levels of power (watts or W), voltage (volts or V), and resistance (ohms or Ω).
Every electrical circuit, irrespective of location or size, has four essential components:
An energy source (AC or DC)
A conductor (wire)
An electrical load (device)
At least one controller (switch)
Ultrasonic and Partial Discharge Testing
Partial discharge (PD) will eventually lead to total insulation failure of medium and high voltage electrical insulation, which in turn can cause unplanned outages and downtime.
When insulation breakdown occurs in medium and high voltage electrical equipment due to partial discharge and corona, the phenomena will produce sound waves that Ultrasonic Testing (UT) can detect.
Ultrasonic testing is performed without disruption to plant or facility operations, and is a non-destructive, non-invasive, predictive maintenance tool.
Partial discharge typically occurs in systems operating at 3 kilovolts (kV) and higher. However, PD can occasionally manifest at lower voltages, i.e., in variable speed drive (VSD) or variable frequency drive (VFD) motors and low voltage (LV) designs.
Partial Discharge (PD) can be classified into 3 main types:

Internal Partial Discharge, Occurs inside insulation

Surface Partial Discharge, tracking across insulation

Corona Partial Discharge - a sharp electrode into gas
Ultrasonic Sensors
Many failures and repairs that commonly occur in an industrial setting can be prevented with ultrasonic sensor technology, a highly effective, predictive maintenance method. In electrical equipment, ultrasonic sensors can detect problems including corona, arcing, and tracking.
Ultrasonic sensors designed with the right technology and software can be used for condition monitoring and predictive maintenance. This will minimize production downtime, improve quality control and safety, and decrease man-hours by improving troubleshooting capabilities.
Organizations must ensure assets are equipped to not only to cope with the rigors of today’s production schedules, but tomorrows' and beyond.
The ability to gain insights into the status of critical electrical assets is essential for those responsible for maintaining service uptime. Regardless of industry, ensuring reliable power uptime is key, and changes in asset conditions such as vibration or temperature can indicate potential issues that require attention.
The methods used to gain such insights can vary, some opting for occasional or periodic condition inspection, whilst others warrant continuous, permanently installed condition monitoring systems.
High Potential Testing
High potential testing, or HiPot testing, involves the application of high voltage to a piece of equipment under test. Usually utilizing voltages much higher than that which the equipment would experience in the normal course of its use in order to stress test the insulating materials (dielectric components) in the equipment.
This type of test can detect if said insulating material is sufficient and that no faults have occurred in either the manufacturing process or during operation that would render the equipment unsafe to an end-user.
Megohmmeter Testing
Tests with a Megohmmeter, or “megger” as they’re commonly referred to, are performed in order to test extremely high resistances where a regular ohmmeter would be insufficient. Most commonly these tests are performed to check the condition of electrical insulation.
These tests are conducted by introducing an incredibly high voltage low ampule direct current (DC) to the machinery, wiring, or insulation under test. Megohmmeters can be either battery operated or generator operated. and despite the high voltages in use, usually present very little danger to the user owing to the low current involved.
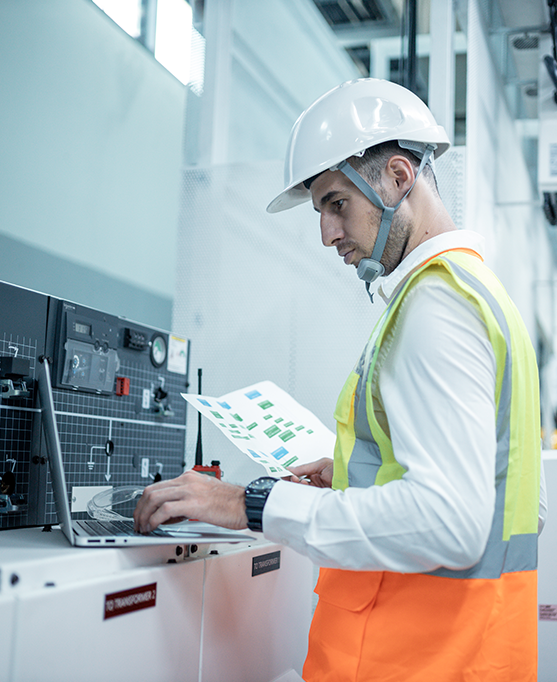
Infrared Cameras and Windows
Infrared cameras (also referred to as thermographic cameras, thermal cameras, or thermal imagers) are a subtype of camera technology that is able to detect infrared radiation and capture images in the infrared range of the electromagnetic spectrum. The term 'infra' is Latin for 'below', therefore, infrared literally means to be 'below red'. Thermal energy or heat energy is visible in this spectrum.
For many years, the accepted ‘best practice’ for detecting faults within electrical infrastructure has been via temperature measurement using a preventive maintenance program in the form of periodic thermal imaging inspections. Typically, these are performed at scheduled intervals such as annually, or quarterly. The frequency of inspections is varied depending on the industry, environment, and nature of the organization.
Inspections are carried out by electrical personnel and often utilize a combination of an infrared thermal imaging camera and a thermal ‘window’ to examine electrical asset status.
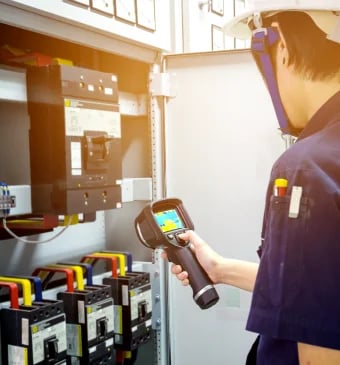
Thermal images are an easy way to identify apparent temperature differences in industrial three-phase electrical circuits, compared to their normal operating conditions. By inspecting the thermal gradients on all phases, technicians can quickly spot performance anomalies on individual legs due to unbalance or overloading.
When combined with regulations such as NFPA 70E/B, this approach has historically provided a satisfactory approach to identifying faulty or loose connections in electrical distribution systems. However, the reality of carrying out a thermal inspection once per year would equate to monitoring <1% of available time, leaving a significant reliance on luck in order to identify a potential issue whilst the inspection is carried out.
As a preventative condition-based method there are several weaknesses in the use of thermal cameras and windows for the detection of electrical faults such as:
Limited inspection frequency
Compromised view or line of sight issues
Data is not integrated or real-time
Dependent on the thermographer skillset
Window transmission degradation / replacement
Expensive over asset lifetime
Safety issues place the operator at risk
Difficult to detect faults at low load
Infrared Sensor Technology
Modernizing existing electrical infrastructure including low voltage (LV) and medium voltage (MV) switchgear, and motor control centers (MCC's), does not necessitate the requirement for new equipment.
With innovations in IIOT sensors and digitization, electrical engineering personnel now have the option to select alternative, cost-effective solutions that will deliver greater benefits. These include enhancements to personnel safety and real-time condition monitoring that enables higher performance and reliability for a facility.
The ability to place condition monitoring sensors permanently inside electrical panels or equipment is quickly becoming adopted as the superior choice of technology over the use of thermal cameras for inspection due to the growth of IIOT and the increasing need for 24/7 condition data. For new build facilities, there is a growing requirement that sensors are designed into the infrastructure to avoid building in obsolescence and future-proof equipment.

Infrared (IR) temperature sensors are well suited to electrical environments due to being both non-contact and non-powered. They emit an infrared energy beam focused by a lens onto a surface to detect the surface or object temperature. The reflected beam is received back in the sensor which converts the energy to an electrical signal that can be displayed in units of temperature.
Infrared (IR) temperature sensors are well suited to electrical environments due to being both non-contact and non-powered. They emit an infrared energy beam focused by a lens onto a surface to detect the surface or object temperature. The reflected beam is received back in the sensor which converts the energy to an electrical signal that can be displayed in units of temperature.
Research shows that 'poorly maintained switchboards' are 62% more likely to fail. This highlights how a digitized approach is key. Utilizing the latest sensor technology will enable continuous monitoring and data collection across all electrical infrastructures. The ability to not just identify, but predict electrical faults before they occur helps ensure two key advantages: increase personnel safety and enhance business continuity.
Below are some advantages of thermal monitoring utilizing infrared sensor technology:
Non-contact and non-powered sensor technology
Sensors monitor inside equipment 24/7
Integrated real-time temperature data
Reduce OPEX and maintenance costs
Approx. 70% increased fault detection
Lowers risk and improves operator safety
Digitizes and optimizes
maintenance
Greater ROI than thermal imaging inspections
Benefits of Condition Monitoring
Thermal condition monitoring provides a multitude of benefits to an end-user versus periodic inspection techniques. Periodic electrical inspection requires engineers to work within close proximity of electrical equipment to carry out scheduled routine checkups of power systems for either existing or potential faults.
Continuous condition monitoring provides the end-user with 24/7 protection of their equipment all year-round, minimizing the risk to both personnel and machinery by providing real-time data on the condition of that machinery (whether it be oil quality, thermal monitoring, or electrical signature analysis). This ultimately reduces the operational expenditure for maintaining that machinery while maximizing uptime.
In addition to this, condition monitoring can help to start, or further your organization’s digitization efforts through the constant acquisition and logging of condition data.
Statistics that demonstrate the advantages of condition monitoring:
Decrease maintenance costs
Reduction in power outages
Increased electrical fault detection
Savings via predictive maintenance
Assuming operational uptime of 8,750 hours per year, and an average maintenance inspection time of one hour per item of equipment, periodic inspection only covers 0.3% of operational uptime; leaving 99.7% reliant on luck that a fault does not develop to the point of failure, compared to the 100% coverage 24/7 monitoring provides.
This allows your maintenance personnel to not only be aware of conditions in the moment, but track changes over time and potentially identify patterns before they become problematic.
The Advance of Condition Monitoring Technology
Condition monitoring is not an especially revolutionary idea. It has existed in one form or another since the industrial revolution. Machinery has long had readouts, and gauges to inform users as to its operating state. Early examples would be mercury thermometers and analog pressure gauges, but while the readouts would provide continuous data, a human being was required to read and log that data.
The same can be said of later technologies that provided status indications via light panels or digital displays. The interfaces became simpler, and easier to interpret but still required human involvement to read and log the data.
For hazardous applications, condition monitoring could be done semi-remotely through a control room separate from the potential dangers, but still requires manning during all periods of operation.
However, given the capital and operational expenditures involved in implementing such a solution, this is not a practical or cost-effective solution for everyone.
Modern, fully connected digitized continuous condition monitoring techniques can constantly read, acquire, log, andlog, and most importantly now analyse condition data without any human intervention past the point of installation. The right technologies can provide local and remote alarms in the event of a potential hazard utilizing the IIOT framework to keep key personnel aware of local conditions at multiple points no matter where those personnel might be in the world.
Condition Monitoring Summary
The benefits of condition monitoring for electrical infrastructure are myriad. 24/7 real-time data collection using permanently installed sensors will provide organizations with constant information on the condition of its equipment for 100% of its operational uptime while maximizing that very same uptime by ensuring timely fault detection via predictive means, as opposed to reacting to a fault that may already be causing problems.
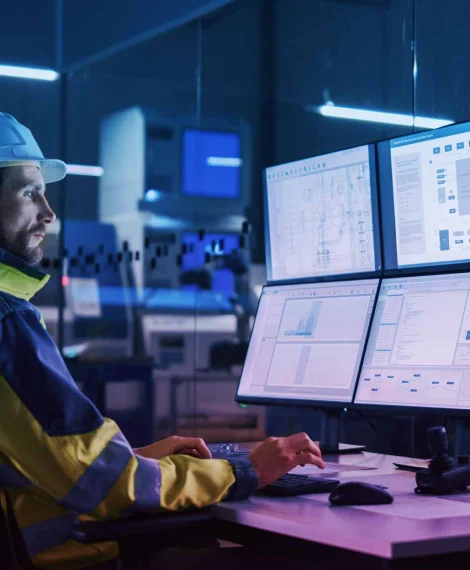
-
Uniformity Of Data
-
Increased Asset Life Expectancy
-
On-Going Added Value
-
Optimized Maintenance Resources
-
Asset Digitization And Analysis
-
Enhanced Facility And Operator Safety
-
Increased Uptime And Efficiency
-
Reduced Opex Costs
-
IMPROVED PRODUCTIVITY
The remote nature of condition monitoring systems helps to ensure the safety of your on-site personnel by minimizing their interaction with potentially dangerous electrical equipment.
By installing remote condition monitoring technology into your organization’s critical infrastructure today, you are stepping towards tomorrow, not only by building in resilience but also by increasing the digital readiness of your organization and preparing or improving its readiness for the expanded IIOT world of the future.
Ensure your electrical infrastructure is equipped with the vital sensor technology required to future-proof it for years to come. Without 24/7 monitoring organizations will be unable to reap the tangible and immediate benefits that come with adopting thermal condition monitoring.
Detecting any potential electrical faults before they develop into serious problems, increases the reliability and resilience of your equipment, and in addition, extends the life span of your organization’s critical assets.
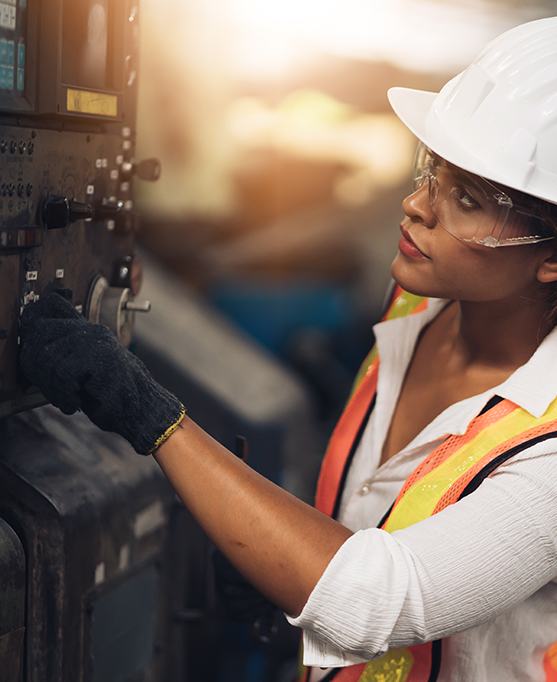